Academic research
CAD - Siemens NX, Solidworks
CFD - Simcenter STAR-CCM+
FEA - Siemens NX
My thesis has proven to be one of the greatest challenges I have encountered so far. This being a real engineering challenge, I had to push myself to the limit concerning math and physics. The topic of my research, virtual design, is a very broad and fairly new domain within design. Together with my supervisors, it was decided the topic should focus on computation fluid dynamics (CFD) simulations.
'Exploration of virtual design in Simcenter 3D: influence of CFD optimizations on a Formula Student race car'

Wind tunnel testing of Polestar 3 (youtube.com/watch?v=EzC0K8BeH6Y)
Simulations are performed to predict the performance of a design or improve a design without investing in several physical prototypes. CFD simulations can predict the behaviour of fluids and gases. A typical application of CFD is virtual wind tunnel testing. Whereas it is expansive to do wind tunnel testing, a virtual model of the car or aeroplane can be simulated in various conditions. This means designers and engineers can already predict and improve a vehicle's performance before physical (and often expansive) prototypes are made.
How to approach simulations as a designer?
As most engineers are not designers and vice versa, it proved to be a real challenge to use CFD software and especially optimisations for a car designed through surface modelling techniques. The outcome of my research proved a method able to use CFD optimisations for a design constructed mainly with splines. This is called the design process for virtual optimisations and follows some guidelines. These guidelines could be a useful way for both engineers and designers to communicate, cooperate and improve their designs.
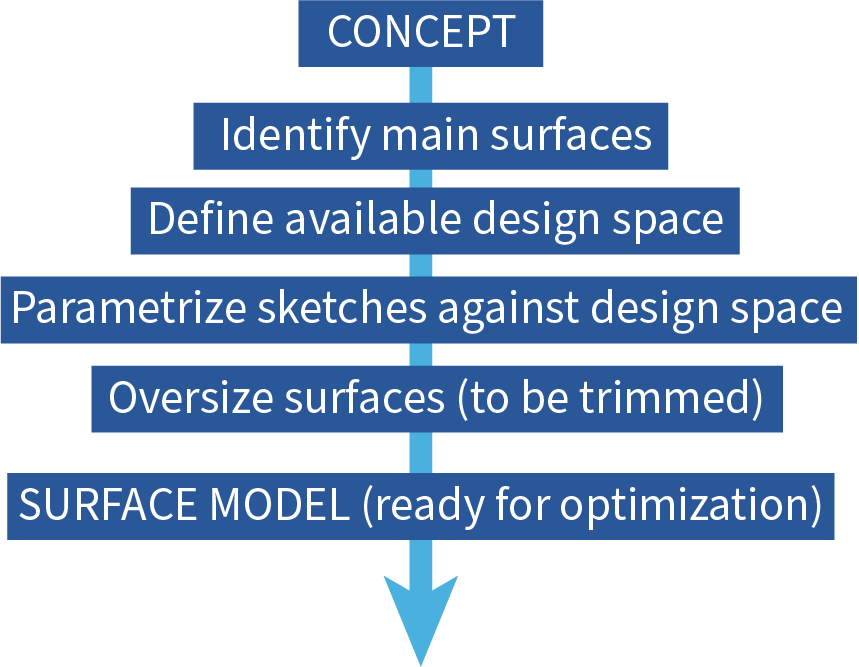
Design process for virtual optimisations
The research is further presented in the following video (Dutch) and can be consulted via Ghent University's Library.